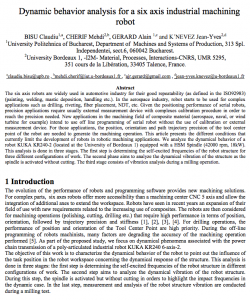
Dynamic behavior analysis for a six axis industrial machining robot
Today I read a published paper “Dynamic behavior analysis for a six axis industrial machining robot”
The abstract is:
The six axis robots are widely used in automotive industry for their good repeatability (as defined in the ISO92983) (painting, welding, mastic deposition, handling etc.). In the aerospace industry, robot starts to be used for complex applications such as drilling, riveting, fiber placement, NDT, etc. Given the positioning performance of serial robots, precision applications require usually external measurement device with complexes calibration procedure in order to reach the precision needed. New applications in the machining field of composite material (aerospace, naval, or wind turbine for example) intend to use off line programming of serial robot without the use of calibration or external measurement device. For those applications, the position, orientation and path trajectory precision of the tool center point of the robot are needed to generate the machining operation. This article presents the different conditions that currently limit the development of robots in robotic machining applications. We analyze the dynamical behavior of a robot KUKA KR240-2 (located at the University of Bordeaux 1) equipped with a HSM Spindle (42000 rpm, 18kW). This analysis is done in three stages. The first step is determining the self-excited frequencies of the robot structure for three different configurations of work. The second phase aims to analyze the dynamical vibration of the structure as the spindle is activated without cutting. The third stage consists of vibration analysis during a milling operation.